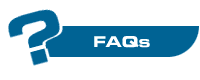
Having a burning question? Chances are some one might have asked the same
question before. Here is a collection of frequently asked questions to
our tech support through e-mail and phone calls. Of course, if you
don't see your question answered here, please
send us a note or call our tech support hotline at 1.800.653.9970.
General Questions
General Technical
Support Questions
Digital Products
Analog Products
Serial Products
Software Questions
Sub Device Ids
Mean Time Between Failures Information
Using Products with Laptops and other mini-systems
General Questions:
Do you have products that support the 3.3 volt PCI bus specification?
How would I go about using your products in a laptop?
While we do not currently make any products that support
typical laptop bus protocols (PC Card, PCMCIA), we have found a way to use our PCIe products with a laptop
by utilizing an expansion system.
Our PCIe products (including PCIe to PMC adapter) with the PCIe expansion system mentioned below, should work with a Laptop.
We have tested it in our lab and it worked fine.
Cabled PCI Express for Desktops and Laptops: http://www.magma.com/expressbox-1
<back to top>
Since upgrading to a Windows 64 bit OS, I seem to be having problems with transferring data.
Some General Standards products have a bus interface chip that uses
32 bit registers for DMA transfers. If your system has more than 4GB of RAM and you are using a 64 bit version of Windows,
there is the possibility that a DMA buffer address could be beyond the 4GB limit of the 32 bit registers. Try temporarily
reducing the amount of RAM in the system to 4GB or less. If your transfers now work properly, contact General Standards
Technical Support to find out about software work-arounds for this issue. Generally, this has not been an issue on Linux
operating systems.
<back to top>
I am looking for MTBF (mean time between failures) information for your products.
How do I contact technical support and when should I call?
If, after reading the manual and the relevant
FAQ help files for your product, you are still experiencing difficulties
installing or using your product, call the technical support hotline. Please
try to be at your computer with your manual, software, and product.
Technical support can be reached at 1.800.653.9970, 8:00AM-5:00PM CST,
Monday through Friday, or email your questions to a
member of our tech support team!.
<back to top>
My design is almost perfect, but I really need to change one small thing.
Can you do this for me?
I have to write my own application, do you have any sample
programs to help?
Yes! We can supply sample programs that
contain commented code that you would need to include with your
application to make calls to our driver. For DOS users there are
also several types of sample programs. <back to
top>
What is PC/104 Express?
General Technical Support Questions:
Do your cards come with a factory warranty? If so, what procedures need
to be followed in an event of failure, and who would we need to contact for repair
services.
Boards have a one-year parts/labor warranty. GSC may choose to repair or
replace a board at its option. Turnaround is typically one to ten working
days. Customer pays for shipment to GSC; GSC pays for return freight with
same delay. GSC disclaims any warranty for any particular application and
is not responsible for any consequential damages. Out of warranty repair is
available at one-third list price for the board; replacement price is one-half
list price.For repairs, RMAs or returns, please
contact a member of our returns team! <back to top>
How do I determine what board I have?
There is a label on the card that indicates the model and serial
number followed by a Revision letter located on the board as part
of the copper or silkscreen. <back to top>
I've lost my Manual. How can I get another?
My system has a PCI Bridge and the General Standards card will be located
downstream. Is their any special configuration I need to be aware of?
Are the PC104-Plus cards assigned specific communication signals?
PCI Device and Interrupt Assignment for PC104-Plus
In the PC104-Plus stacking configuration, each of up to four modules is assigned specific communication signals as described
in Paragraph 3.2.2 of the PC/104-Plus specification, Version 1.2. Because of the stack-through nature of the bus, slot-specific
signals are duplicated for each plug-in module, and include IDSEL[3:0], CLK[3:0], REQ*[2:0], GNT*[2:0] and INT[A-D].
In this product, the device identification and interrupt lines are controlled by the position of the octal switch located at one edge
of the module (Figure 1.1-1). The exact relationship or mapping of switch positions and slot-specific signals may vary among
manufacturers of PC104-Plus motherboards. Keep in mind; some manufacturers may assign one of these slot-specific signals
(slots) to a device located on the processor board, limiting the number of modules that can be stacked thus, a conflict with one of the devices in the stack can occur. Should this happen, refer to the motherboard documentation on how to
resolve it.
My original card is working and the new card is not functioning properly. What may be the problem?
Verify that you have not set reserved bits. General Standards utilizes reserved bits to add new features as required by customers.
Can you give me the specifications of the CPU board that would support your cards?
We have tested the following CPU boards:
A. Winsystems, EBCTX Plus
B. Versa Logic, VSBC8
How can I change IRQs assigned to my PCI communication board?
Because the BIOS allocates resources for the PCI bus, IRQs can
only be changed by moving your adapter to a different PCI slot.
If you have only one free IRQs or no IRQs available the
IRQs assigned to the PCI adapter may not change.
<back to top>
I have an older VME card and was wondering if you had a replacement on
another form factor?
We have newer cards on PCI, PMC and cPCI that can replace most VME boards
manufactured by General Standards Corporation.
<back to top>
What is RS-232?
Probably the most widely used communication standard is RS-232. This
implementation has been defined and revised several times and is
often referred to as RS-232 or EIA-232. The most common
implementation of RS-232 is on a standard 25 pin D sub connector,
although the IBM PC computer defined the RS-232 port on a 9 pin D
sub connector. Both implementations are in wide spread use. RS-232
is capable of operating at data rates up to 20 Kbps / 50 ft. The
absolute maximum data rate may vary due to line conditions and cable
lengths. RS-232 often operates at 38.4 Kbps over very short
distances. The voltage levels defined by RS-232 range from -12 to
+12 volts. RS-232 is a single ended interface, meaning that a single
electrical signal is compared to a common signal (ground) to
determine binary logic states. A voltage of +12 volts (usually +3 to
+10 volts) represents a binary 0 and -12 volts (-3 to -10 volts)
denotes a binary 1.
<back to top>
What is RS-422?
The RS-422 specification defines the electrical characteristics of
balanced voltage digital interface circuits. RS-422 is a
differential interface that defines voltage levels and driver /
receiver electrical specifications. On a differential interface,
logic levels are defined by the difference in voltage between a pair
of outputs or inputs. In contrast, a single ended interface, for
example RS-232, defines the logic levels as the difference in
voltage between a single signal and a common ground connection.
Differential interfaces are typically more immune to noise or
voltage spikes that may occur on the communication lines.
Differential interfaces also have greater drive capabilities that
allow for longer cable lengths. RS-422 is rated up to 10 Megabits
per second and can have cabling 4000 feet long. RS-422 also defines
driver and receiver electrical characteristics that will allow 1
driver and up to 32 receivers on the line at once. RS-422 signal
levels range from 0 to +5 volts. RS-422 does not define a physical
connector.
<back to top>
What is RS-485?
RS-485 is backwardly compatible with RS-422; however and is optimized
for multi-drop applications. The output of the RS-422/485 driver is capable
of being Active (enabled) or Tri-State (disabled). This capability allows
multiple ports to be connected in a multi-drop bus and selectively
polled. RS-485 allows cable lengths up to 4000 feet and data rates
up to 10 Megabits per second. The signal levels for RS-485 are the
same as those defined by RS-422. RS-485 has electrical characteristics
that allow for 32 drivers and 32 receivers to be connected to one line.
This interface is ideal for multi-drop or network environments.
RS-485 tri-state driver (not dual-state) will allow the electrical
presence of the driver to be removed from the line. The driver is in a
tri-state or high impedance condition when this occurs. Only one driver
may be active at a time and the other driver(s) must be tri-stated.
RS-485 does not define a physical connector.
<back to top>
Will standard off the shelf cables work with my RS-422/485 Board?
No. These cables are made with RS-232 in mind and do not
conform to the pin-out for RS422-485. It is best to contact us for
cabling information.
<back to top>
What is the maximum distance I can run my cable with your RS-232
cards and RS-422/485 cards?
The specification for RS-232
calls for a maximum distance of 50 feet at 20Kbps and the RS-422/485 specification
calls for a maximum of 5000 feet at 9600Bps. Data rates are a function of
the distance of the cable. The shorter the cable length the higher the data
rate that can achieved.
<back to top>
How do
you provide uniform cooling at various altitudes?
Cooling:
To provide uniform cooling at various altitudes, approximately the same mass-flow
of air is required regardless of atmospheric pressure. This means supplying
twice the volumetric air flow at one-half atmosphere, 10-times at 1/10 atmosphere,
etc.
Interconductor Spacing:
The arcing threshold between conductors drops with reduced atmospheric pressure.
Conformal coating is usually the remedy for this. Conformal coating is expected
to raise the arcing threshold such that the board should work up to 80,000
feet. The connector will not be conformal coated; however, it probably has
a voltage rating of over 100 Volts at sea level.
Digital Products:
I would like to perform a loop-back data test on my HPDI32 to validate
the card is working properly. I write a data pattern to the FIFO, but when
I read back from the FIFO, I don't get my data.
Am I doing something wrong?
It is certainly possible to do a loop-back test on your HPDI32!
A little information about how the on board FIFOs work is warranted here.
There are effectively two 32 bit wide, 32K deep FIFOs (for the -256K model)
on the card, one for transmit data and one for receive data. The logic on the
card looks for an access to local offset 0x18 and checks the Read/Write line
from the PCI interface. If the R/W line indicates a write is taking place,
the logic puts that data in the transmit FIFO. If the R/W line indicates
that a read is taking place, the logic reads a word from the receive FIFO.
This confuses a lot of people because they want to write to the FIFOs at offset 0x18,
then do a read of 0x18 and don't understand why they don't get back the data
they wrote. Their data is actually still sitting in the TX FIFO. Here is a way
to loop the data from transmit to receive, which involves a just a few steps:
1) Make sure any external cables that could drive the cable are disconnected,
2) Put test data in the transmit FIFO,
3) Enable transmit in the Board Control Register,
4) Enable receive in the Board Control Register,
5) Set the Start_Transmit bit in the board control register (wait for this bit
to clear itself before proceeding to read) and
6) Read the now transferred data from the receive FIFO (again at offset 0x18).
That's it! You should now be able to test your loop-back data from the receive FIFO.
<back to top>
Who supplies cable clocks and when?
When the HPDI32 card is set to be a transmitter, the card supplies
a transmit clock on pins 1 and 2 of the cable connector
(from the factory, this transmit clock is installed at 20Mhz)
that is synchronous with the data output. When the HPDI32 is in
receive mode, the card expects to receive a clock on pins 1 and 2
of the cable connector. The HPDI32 uses this clock to register data.
If no clock is provided, no data will be saved to the receive FIFO.
<back to top>
The factory supplied transmit clock is the wrong speed for
my application. What are my options?
Usually accommodations can be made when a card is ordered to
obtain a different transmit clock frequency. Simply let your sales
person know the frequency you need, and we will give you a special
part number to order with. If you have already received your cards
and need to change the installed clock, see the Hardware Configuration
section of the User's Manual for detailed pin-out information on the
clock chip. This chip can be changed in the field to accommodate many
different frequencies. Maximum reliable speed for the RS485 version
of the card is 26Mhz, where the maximum speed for the PECL version
of the 40Mhz, assuming a reasonable length cable.
<back to top>
I really just need a simple way to save data into my HPDI32
card. Is there a way to implement a simple interface utilizing
a "data valid" type signal to clock my data in?
Yes! The easiest way to implement a simple interface is to tie
the Status Valid line (pins 7 and 8 on the cable) to a logic low
and tie the Frame Valid line (pins 3 and 4 on the cable) to a
logic high. Then the Line Valid signal (pins 5 and 6 on the cable)
becomes functionally a "data valid" signal, as when this line
is high, a data word is clocked into the card on each clock cycle.
Alternatively, you may tie Line Valid and Frame Valid together to
act as a data valid when these lines are pulled high.
Do make sure to tie Status Valid low, though, since if this line
floats, it can cause erroneous data collection from the cable.
<back to top>
I am trying to program the FIFO almost full and almost empty flags.
I write a value to these registers, but when I write/read data
to/from the FIFOs, the flags don't change where they should.
In order for the value in the programmable FIFO registers to be loaded
, you need to perform a FIFO reset after writing these registers.
This is accomplished be setting the FIFO reset bits(s) in the board
control register. Be careful not to do a board reset, as this will
cause the FIFO programmable almost registers to be cleared.
<back to top>
Analog Products:
What are the advantages of high-resolution sigma-delta ADCs?
The advantages of high-resolution ADCs include inherent antialiasing and high linearity. Static accuracy and broadband noise however, are not significantly improved by the Sigma-Delta (or Delta-Sigma) architecture. In fact, some Delta-Sigma ADC products exhibit huge offset and gain errors of several percent or more, but are considered entirely suitable for acoustic applications.
For example, the data sheet (attached) for the newly released 24-Bit 256KSPS AD7768 converter from Analog Devices indicates a broadband SINAD of 107dB (17.5 bits ENOB). The supporting input analog networks contribute typically 3-5 dB of additional noise, for a further ENOB reduction of approximately 0.5-0.8 bits.
Minimizing aliasing however, simplifies the improvement of dynamic range through post filtering. For example, a converter with a sample rate of 200KSPS and a useable bandwidth of 80kHz might exhibit a typical SINAD of 105dB (17 bits ENOB). By post filtering the output of the converter to limit the bandwidth to, say 5kHz would decrease the noise by a factor of approximately 4, for a SINAD increase of 12dB to 117dB (or an ENOB increase to 19 bits).
<back to top>
What is a simple, graphical way I can view data received from one of your A/D boards?
To look at the data captured from several of our A/D board products is a
more general purpose software tool called ScopeDSP. It does a good job of
displaying sample data from a previously saved file. It also shows you
signal statistics (RMS values, etc) and can do FFT transformations. Read more about ScopeDSP
<back to top>
How do I set the effective sampling rate on the PMC66-14HSAI4 board?
The PMC66-14HSAI4 board's effective sampling rates are a function of the
register values of the four board parameters: Nvco, Nref, Ndiv-clk, and Ndec.
Please see section 3.4.3 of the 14HSAI4 manual for a detailed description of
how this works. The general problem is to find values for these parameters that
produce a solution to the equations in that section of the manual that yields the
user's desired sampling rate - or if it's not possible to get an exact solution - to
find a solution that minimizes the sampling rate error - so as to get as close as
possible to the user's desired sampling rate. A computer program was written
to allow users to quickly find the best solutions for any desired sampling rate
from 1.000 KHz to 50.000 MHz. The program is called 14HSAI4setup. Click here to download
<back to top>
What's required to install the 14HSAI4setup program?
Download 14HSAI4setup.zip to a computer running
Windows 2000 or later. Unzip the zip archive into any convenient location.
This will unzip into a new folder named "14HSAI4setup". Within that folder
will be an executable file named "14HSAI4setup.exe" and some support files
that are needed by the program. Double-click the icon to run the program.
A shortcut that points to this program can be added to the desktop if desired.
There is no installation. This program may be removed from the computer by deleting the 14HSAI4setup folder, and any shortcuts to it you've created.
(A version of this program that works under Linux is available upon request.)
<back to top>
How do I use this program?
Enter the desired effective sampling frequency in Hertz - samples per second.
(e.g. 10.002 MHz would be entered as "10002000" - an integer without any
decimal point. Enter "0" to terminate the program.) The program will find a
solution, but will sometimes show multiple solutions. If several solutions are
shown note the Fsample(error) results and choose the best one from among
those listed.
<back to top>
What is the latency of the PCI-ADADIO board?
As long as the delay is less
than 5 milliseconds between conversions, the conversion time is only 5 microseconds.
If the time span is greater than 5 milliseconds then the conversion time is
9 microseconds. This is for the 200kHz version of the board.
ADC sampling can be triggered: (a) software, (b) externally through hardware
or (c) by the internal rate generator. For a 200KSPS board, the time from
a trigger to when all four channel values are present in the buffer is 5.Ous.
If a DMA-read is started immediately after the buffer-empty flag falls
(i.e.: when the first values appear in the buffer), total time from a trigger
through PCI four transfers would be 5.5-6 Ous. System delays (not controlled
by the ADADIO) would increase this time.
The latency does not change until you get down to 160 samples per second,
this latency increases to 10.5 to 11.O micro-seconds due to a double-sampling
requirement imposed by the ADC at very low sample rates.
<back to top>
How do I set the sample rate for the PCI 16SDI?
The answer is almost boundless due to the number of variables but
click here
to download an excel document that should be of great help.
<back to top>
How do I "find the board" on the PCI Bus
The answer is to perform
a PCI Configuration Access. You may click here to download
a sample function to do a Configuration Access on X86 machine. Click
here to download a white paper explaining PCI Bridge Compatibility
<back to top>
Serial Products:
What is the maximum speed of my Serial Card?
The maximum data rate is 1 Mbps asynchronous and 10 Mbps
synchronous. This number is the result of a mathematical calculation based on
the on board oscillator value on the card. Actual maximum data rates may vary depending
on cable length, type of driver, operating system overhead, disk activity, etc.
<back to top>
Where can I obtain a user's manual and product specifications
for the Zilog Z16C30 chip used on the Serial I/O boards?
The Zilog web site has the specification and User's Manual for the
Z16C30. The User's Manual covers the serial protocols supported by the
Z16C30.To access the Z16C30 User's Manual (.pdf format) just
click here. Here you can view, search, or print the User's Manual
for the Z16C30.
To access the Z16C30 Product Specification (.pdf format) just
click here
.Here you can view, search, or print the Product Specification
for the Z16C30.
<back to top>
I cannot achieve the baud rate needed for my application using the
factory installed 20MHz clock. What options are available?
The oscillator for the baud
rate generator is socketed so we can easily accommodate any frequency commonly
available.
Practically all boards so far have been shipped with the 20MHz oscillator
since the baud rate generator on the Zilog chip provides a lot of flexibility
in baud rate.
We currently do not charge a premium for installing a special frequency, provided
that it is available from stock at a distributor.
Simply add -nn.nMHz to the model number to specify frequency of the oscillator.
For example, for a PMC-SIO4-256K with a 16MHz oscillator for controlling specify
PMC-SIO4-256K-16MHz.
<back to top>
What
is the difference between the SIO4B/BX/BX2/BXR and the SIO4B/BX/BX2/BXR-SYNC boards (Includes 8 channel cards)?
SIO4B/BX/BX2/BXR:
This is a high-speed serial card that features the Zilog Z16C30 serial controller
chips. This card is best used when the serial protocol will be one of the
"industry standards" such as HDLC/SDLC, asynchronous, isochronous,
bisync or monosync. The Zilog chips will handle the protocol specific overhead
and add/strip extra information from the serial data stream to make it match
the requested protocol. This card offers deep FIFO buffers (up to 32KB) to
help reduce the risk of data loss at high clock rates. The SIO4BX can run
up to 10 Mbits/sec in synchronous protocol modes and 1 Mbit/sec in asynchronous
mode with the software selectable transceivers set for differential (RS422/485)
mode. Single-ended modes, such as RS232 and RS423, are limited to 230 kbits/sec.
Drivers are available for Windows, VxWorks and Linux.
SIO4B/BX/BX2/BXR-SYNC:
This is a high-speed synchronous serial card that basically performs simple
serial to parallel conversion of data. It does not support the high level
protocols like the SIO4BX/Zilog chips and does not add/strip any information
to/from the data stream. This card is best used when the customer is using
a proprietary serial protocol that can be decoded in software or simply needs
to send or receive raw serial data without any of the high level protocol
overhead. This card offers deep FIFO buffers (up to 32KB) to help reduce the
risk of data loss at high clock rates. The SIO4BX-SYNC can operate at up to
10 Mbits/sec with the software selectable transceivers set for differential
(RS422/485) mode. Single-ended modes, such as RS232 and RS423, are limited
to 230 kbits/sec. Drivers are available for Windows, VxWorks and Linux.
Note: The SIO4B and SIO4BX cards are functionally identical except the SIO4BX features software configurable
cable transceivers.
<back to top>
Software Questions:
Sub Device Ids:
Does General Standards provide a means of locating their card on a system bus?
Yes. Please click here to download a
document with subsystem ids listed for all General Standards products.
<back to top>
Do you have sample Windows programs for your cards?
Where can I get the latest Windows drivers?
Is there a way to use your products with
a laptop or some other mini-system that does not provide bus slots?
And as always, if you have an URGENT question, please call 800.653.9970
or 256.880.8787.
|